Case Studies
Motion Drives & Controls Ltd. is a leading distributor and system integrator of web processing, mechanical power transmission and safety products. We build strong relationships with our customers and supply partners whilst applying our vast knowledge and experience to deliver tailored Engineering and component solutions.

Innovative Guided Unwind Stand for Enhanced Web Processing
Motion Drives & Controls has engineered a bespoke guided unwind stand to optimise the processing of glass fibre veil web materials. Aimed to supersede an outdated manual system, this new solution was meticulously designed to improve quality, speed, and repeatability, with no margin for extended production downtime.
Coating Line Dual Unwind Upgrade with Closed Loop Control
Motion Drives & Controls was approached by a long-standing customer seeking a solution to replace poorly performing Coremo Brakes on their main coating line. The existing brakes resulted in high levels of scrap due to their non-linear and juddering performance at slow speeds, required for their curing process. In addition to replacing the brakes, Motion Drives & Controls proposed implementing a new closed loop digital tension control system to further enhance the performance of the braking system.
Coremo Brakes Replacement and Digital Tension Control System Upgrade
A long-standing component customer of Motion Drives & Controls was experiencing high levels of scrap due to poorly performing Coremo Brakes fitted to two unwinds on their main coating line. The line needed to run at slow speeds due to the nature of their curing process, and the Coremo brakes were juddering and non-linear when adjusted. Motion Drives & Controls was asked to find a solution to this problem, and they proposed replacing the brakes and adding a new closed loop digital tension control system to improve the performance of the braking system.
Enhancing Unwind Tension Control in Adhesive Tape Converting
A project was undertaken to overhaul an unwind station as part of an adhesive tape converting line. The existing setup was failing to maintain proper tension control, negatively impacting the quality of the products.
Gloucestershire Printing Company - Mabeg Reel to Sheet Feeding Machine Upgrade
The project was initiated by a printing company in Gloucestershire that was experiencing high maintenance issues with their Mabeg reel to sheet feeding machine. The original caliper brakes were causing the system to produce incorrect sheet lengths, and the maintenance team was being called to the machine daily. The machine builder confirmed that the original hydraulic caliper brakes were being discontinued, necessitating an upgrade.
Holistic Approach to Production Line Improvement
In late 2018, Motion Drives & Controls was approached by a customer seeking to improve the braking system on one of their production lines. The customer, a specialist in tubing production, was dealing with a significant issue of expensive scrap produced during setup. The tubing produced had a non-permeable membrane added partway through the extrusion process, enabling its use in brown field sites. The project was delayed due to Covid-19 restrictions but was completed in 2021.
Revitalising a 60-Year-Old Slitter Rewinder
The task was to rejuvenate a slitter rewinder that was not performing as expected. The machine, at least 60 years old, was still using many of its original mechanical features, with the exception of some new slitting blades, a changed motor, and brake. The slitter was used to rewind 500 mm diameter multiple slit widths from reels 2.6 m wide and 2.5 m in diameter. The main issues were the density of the reels and the difficulty in separating the slit reels once the wind was complete.
Systems Labelling - TH Dixon Coater Upgrade
To upgrade the existing TH Dixon Coating machine which is critical for supplying this label printing company with its release papers.
In summary the upgrade was to include the following items:
- Replacement of the safety chucks on each of the three turret unwinds/rewinds
- Replacement of the machine control system including DC motor drives
- Replacement of the old pneumo-hydraulic intermediate web guide system with a modern, fully electric system
- Replacement of the 6-off 3” and 6” diameter airshafts
- Additional dancer to eliminate problem of web speed mismatch between driven laminator rollers and chill rollers
Upgrading Mark Andy 2200 Flexo Press with MAGPOWR Components
Motion Drives & Controls Limited, the Magpowr distributor in the UK, has been working on the Mark Andy 2200 flexo press for the last 27 years. The machine, fitted with Magpowr clutches, brakes and bespoke controls, has been popular in the label printing market. However, the special control boards have become obsolete, and the need for an upgrade path using standard Magpowr components has arisen.
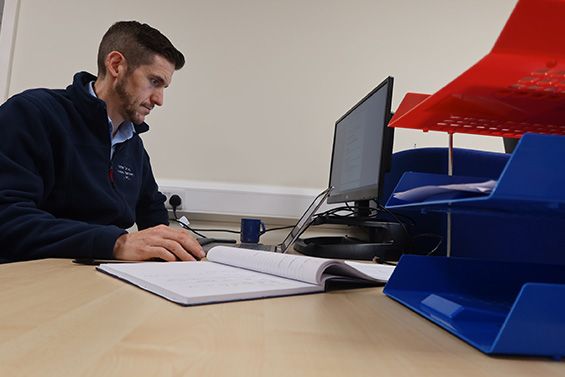